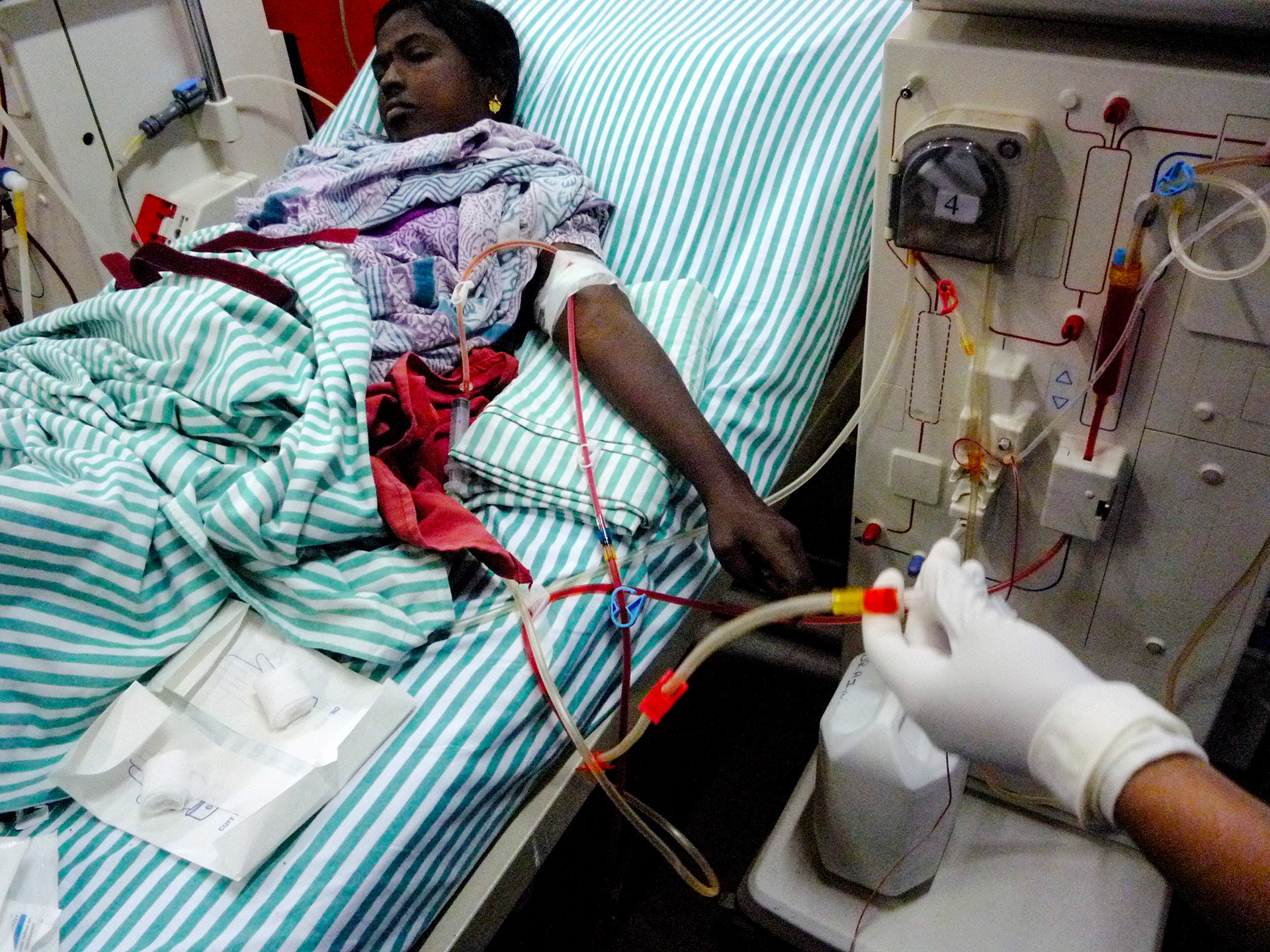
IcarusNova was approached by a startup, Renalyx, which has been focusing on renal healthcare, and was in the process of developing a Dialysis Machine to address the lack of a completely Indian built machine, and compete with the existing market dominated by major players from Germany, Korea, Japan and the USA. The idea was that such a machine built with the 'Make in India' initiative would help bring down the costs considerably for patients undergoing dialysis, as well as the operational costs incurred by the hospitals and private dialysis centres.
To build a machine from ground up required an in-depth understanding of Dialysis as a procedure, the Devices and Machines currently being used ; the Patients undergoing Dialysis ; the Doctors, Nurses, Technicians and Staff members of a hospital or Dialysis centre who are involved in the procedure and have to interact with the machine constantly ; the Service Technicians who have to maintain the machine to ensure the machine performs rigorously for 6 days a week ; the physical environment where all this is playing out in real time; and the mental levels of acceptance on part of the people involved where this has become a part of life for them..
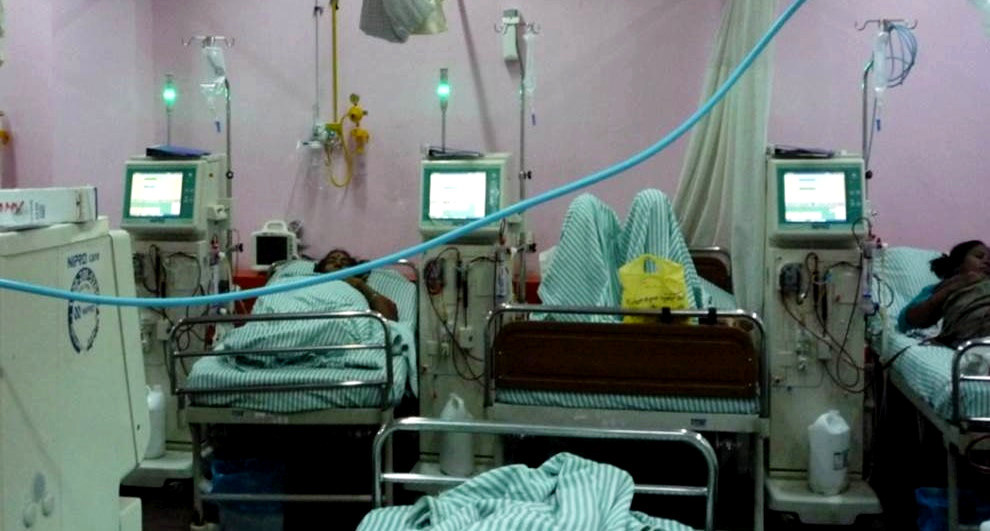
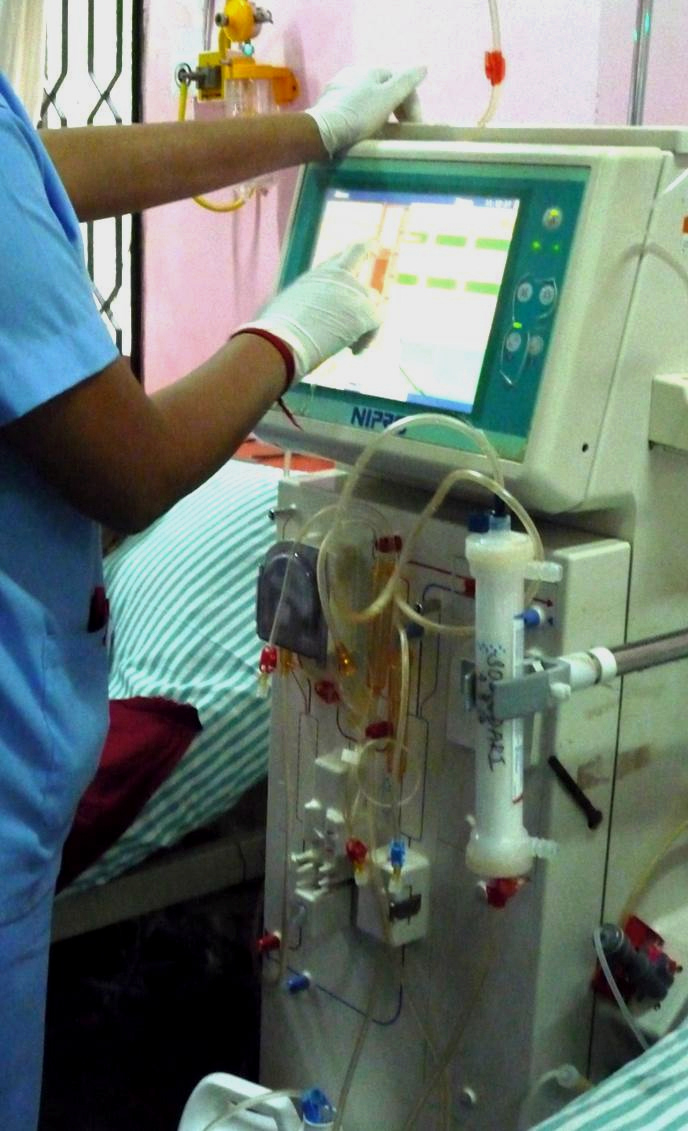
Having spent a considerable time on research, the Nova team observed that the design of the machine needed to incorporate much more than the hydraulics and electronical components which 'run' the device. It also needed to be less intimidating for patients who spend almost 12 hours a week beside one ; provide the nurses and technicians a gentler learning curve for operating the device and, a quicker and easier access to internal components for maintenance and servicing.
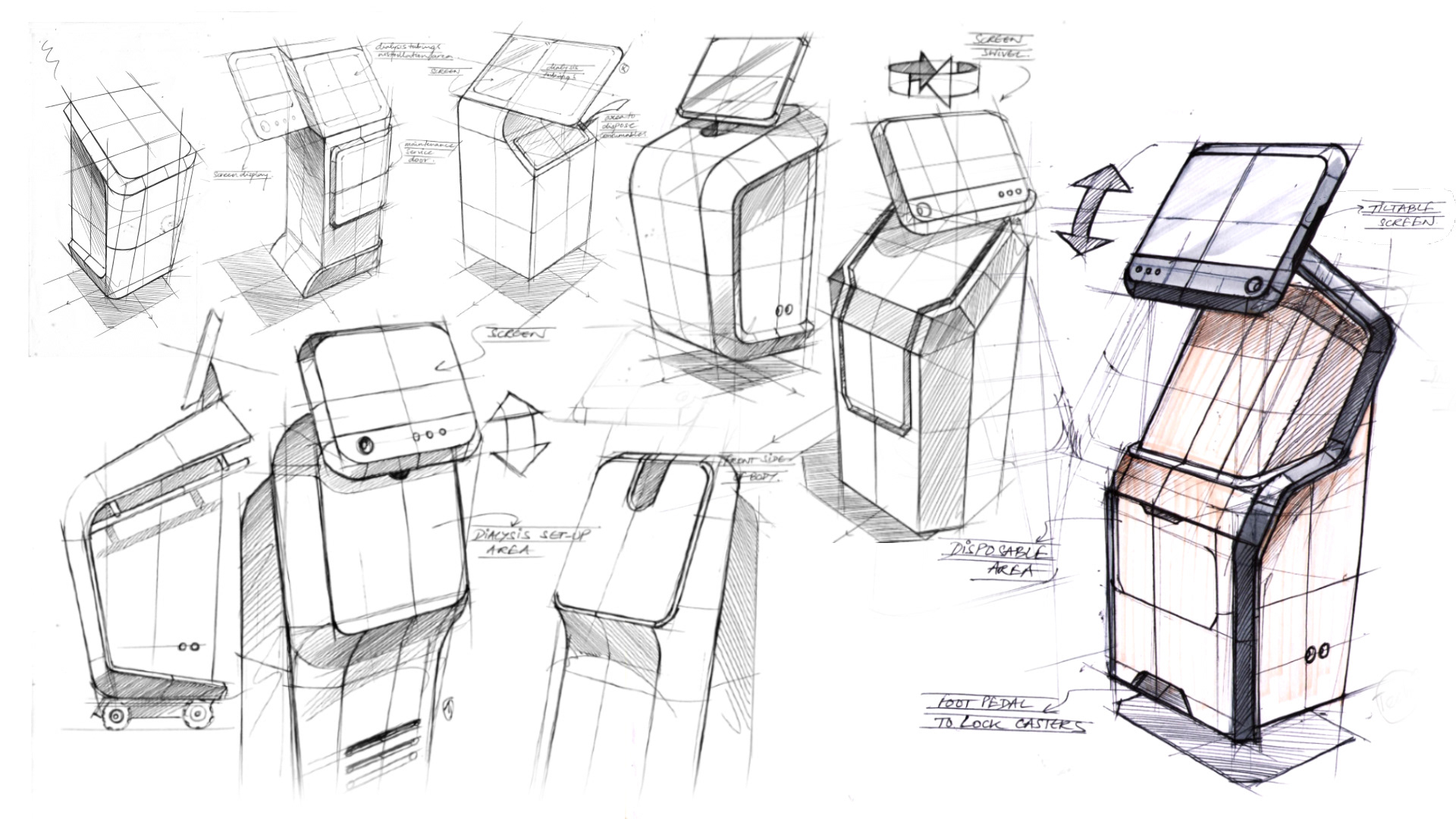
Stage 1 of this project was to work closely with the Technical team of Renalyx, to develop ideal internal layouts of the hydraulical and electronical components, location of Acid and Bicarbonate containers, keeping in mind access for service and maintenance, ideal size of the display screen, functioning of alarms and overall volume, dimensions and footprint. A 'Proof of Concept' of functionality and dimensions was the final result of Stage 1, which laid the stepping stone for Stage 2.
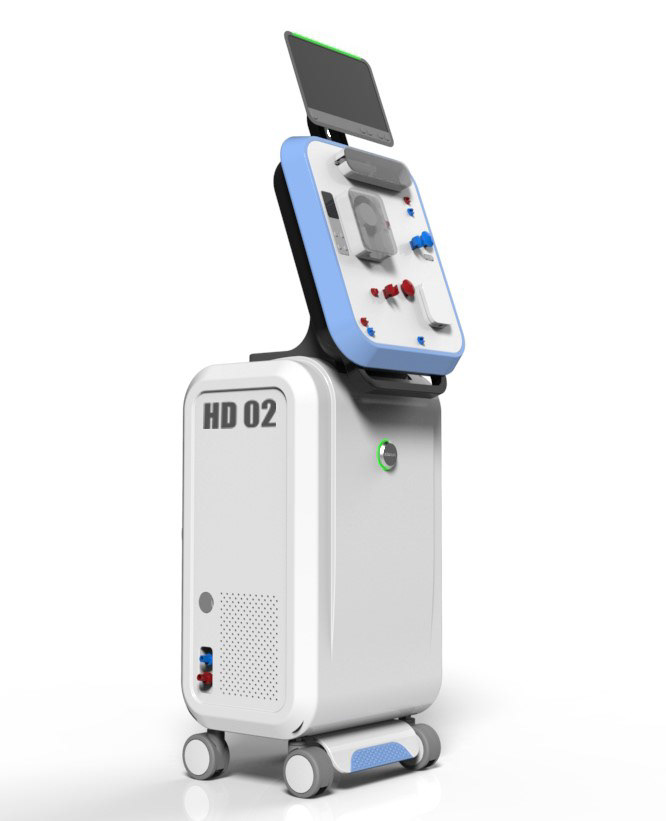
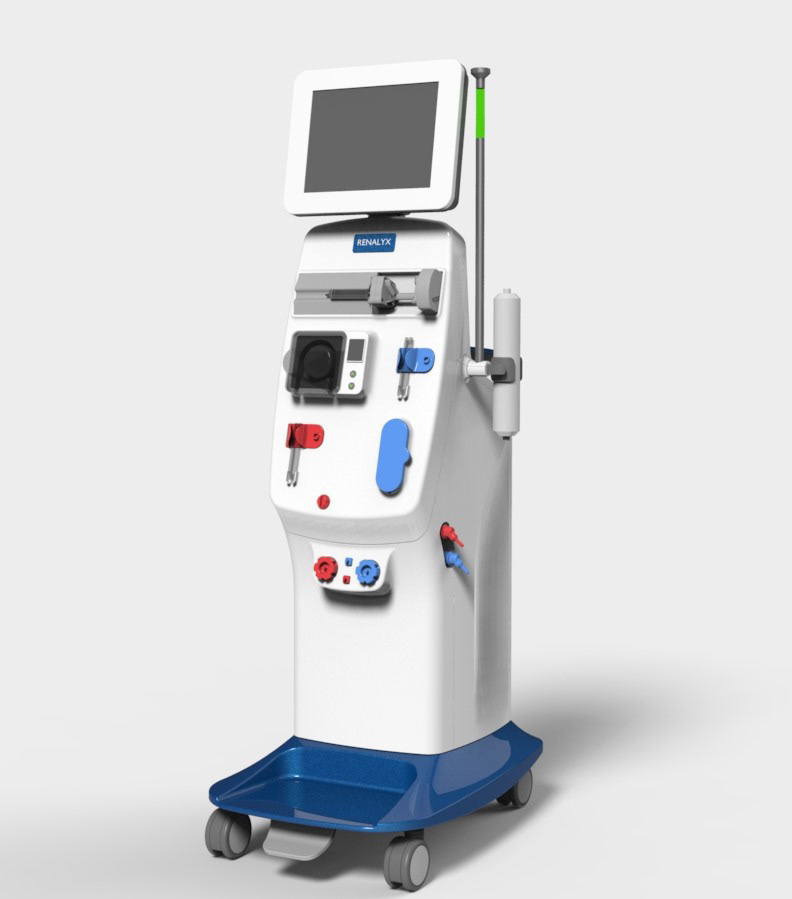
Stage 2 involved the exploration of the final forms, volumes and design details, where the intention was to keep the machine approachable, less intimidating, and comfortable to be around for long periods. Handles on the back for handling and positioning the machine, integrated base for storing containers of Acid and Bicarbonate, easy access to internal components, are amongst the many details and features that have been incorporated in the final form.
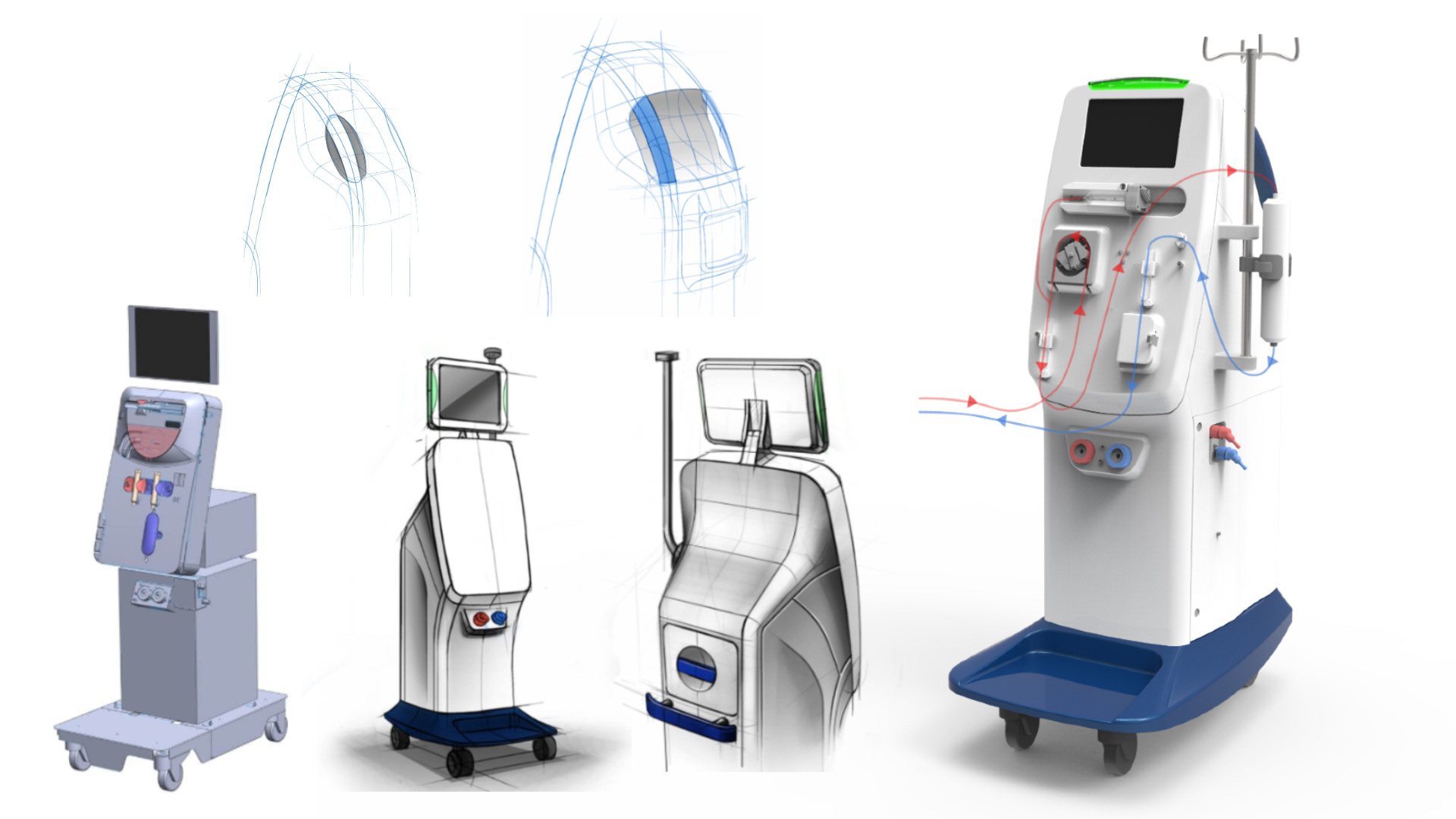
With changes being made to accommodate manufacturability, compliance to ISO standards and guidelines, the final prototype had undergone trials successfully, and was recently unveiled in a Medical Expo in Bangalore.
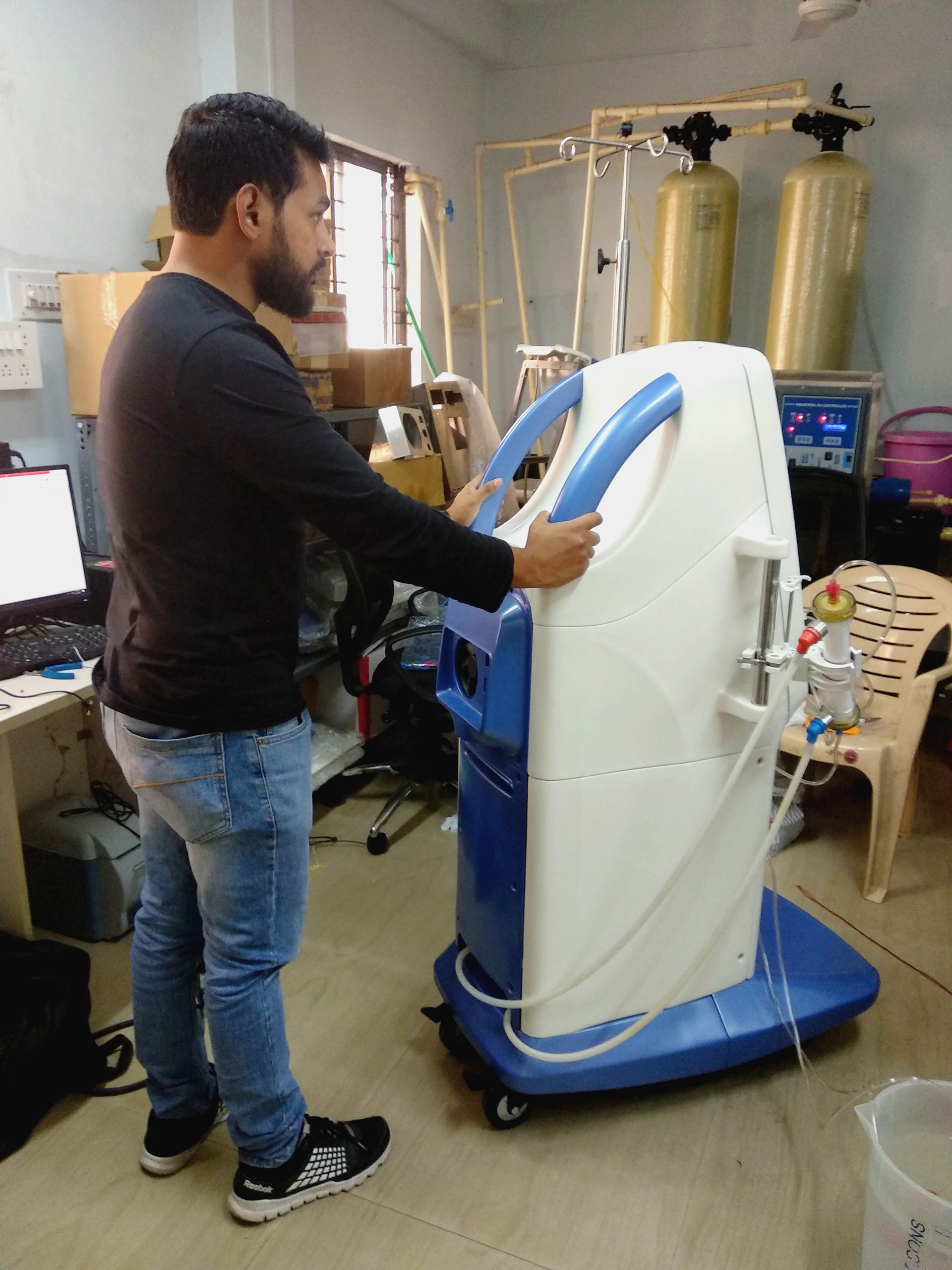
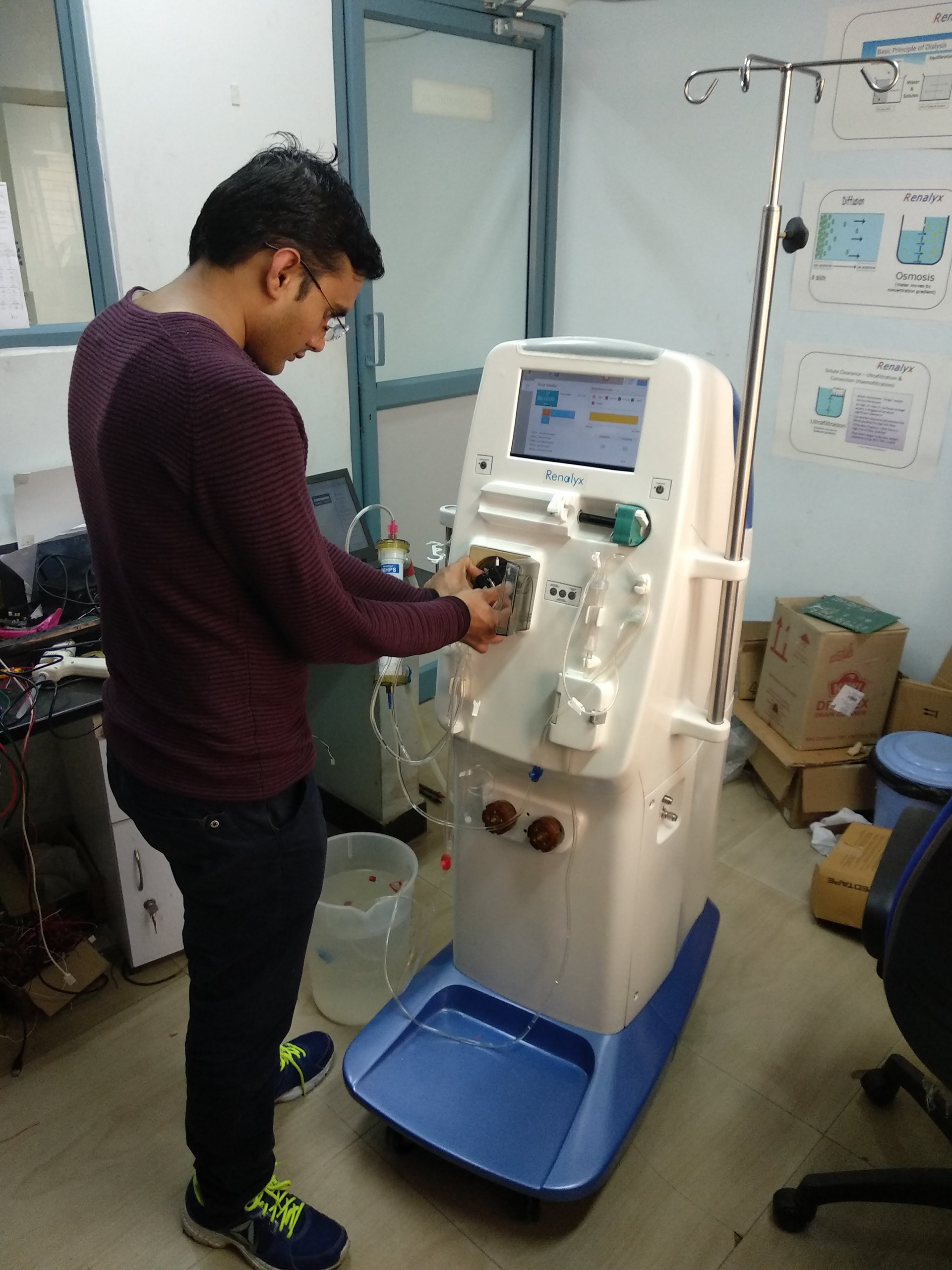